The Most Efficient Ways To Create Bonds For Injection Plastic Molding
Thermoplastic Welding Of Disparate Parts
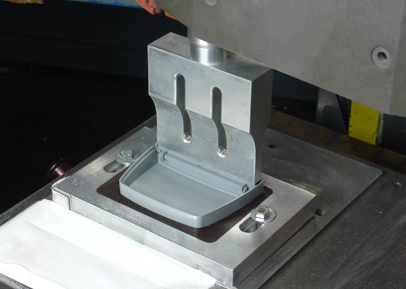
While molds for injection plastic molding can be extremely intricate with many faces, cavities and dimensions, there are always instances where two or more pieces will have to be joined together by other methods. Seams such as these can be a critcal challenge to short and long-term injection molded product integrity as the effects of stress, environmental exposure, chemical exposure, heat/cooling cycles and other events degrade these post-molding production processes. B & B Molded Products recognizes this production reality and offers a number of ways to create enduring physical contact between two injection molded faces. These approaches have different cost-benefit profiles and can be part of our design and manufacturing intake/setup process for any project.
Despite the growing popularity with ways to combine different plastics with other materials like overmolding, insert molding and multi-material (multi-shot) processes, many times more traditional “downstream” assembly techniques are required where different components need to be joined. Examples of these are where components added can’t sustain the higher heat levels of the injection molding process, where more complex assembly is required than can be performed inside the mold cavity.
Sonic: Sonic welding can easily be customized to fit the exact needs of our customers’ specifications. To allow the two pieces to weld together one of the materials will have a raised energy director that creates contact between the two pieces. The energy created in this process melts the two parts together. Sonic welding is much faster than using traditional methods such as snap-fit designs, glue, or screws.
No single welding process fits all requirements. Therefore B & B Molded Products has acquired proficiency in a variety of common welding approaches including:
Spin Welding: Spin welding uses friction between a stationary part and a mobile (spinning) part to create enough heat for the parts to weld together. Spin welding is very fast, efficient, and has high quality results.
Vibration Welding: Vibration welding happens in less than a second, and involves two parts rubbing their surfaces together for an established period of time. This time period is the exact amount of time needed for enough heat to be formed so the parts melt together. Vibration welding is very time efficient and allows for both complex and large parts to be used in the process.
Bonding, Glues and Other Forms of Chemically-Supported Thermoplastic Attachment
We also provide Various types of adhesive bonding. Chemical bonding is the process of adhering parts together by using a chemical adhesive. There are many issues associated with selecting and applying the correct chemical boding agent including:
- Base thermoplastic resin selection
- Processing and post processing (such as coatings/paints, sealants, colorants added, etc.) of the thermosplastic part
- Selection and properties of the chemical bonding agent
- Required surface preparation
- Post-addition of coatings/paints, sealants, etc. over the bonded part
B & B Molded Products has a thorough knowledge of commercial bonding agents and can help our clients select the correct mix of the above factors to achieve their cost-production goals.We can also offer methods of testing these joinery approaches such as seam-level destructive testing with force gages or more straightforward leak testing.