Getting a Second Opinion from a Nearby Injection Molding Problem Solver
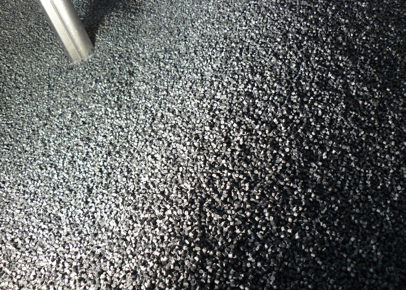
The source of injection molding problems isn’t always easy to determine. Problems that relate to new program startups may be vastly different than those that develop after a program has run successfully, or at least appeared to. Intermittent problems may be the most difficult to diagnose. To help injection molding buyers determine the cause of poor performance, we offer a no cost, process analysis in which we analyze over 50 different parameters most likely to help determine the root cause of any injection molding issue. We analyze all phases of the process including product design, mold design, material selection, machine setup/operation, secondary operations, assembly and logistics. Some of the key symptoms we look for include:
Surface imperfections including streaking, blistering (which may be caused by air entrapment), bubbles, burns, cracking, discoloration and sink marks.Part structural problems which can take the form of delamination, flow marks, gate buildup, warpage and gelling.Process symptoms such as excessive flash, jetting, material leakage, part dimensional inconsistency, mold release problems, shorts, voids and weld lines.
Detection of these and many other symptoms allow us to use our branching analysis to determine first and second tier causes such as material moisture content issues, feed system problems, gate positioning errors, hot runner issues and melt and tooling temperature errors.