Why Reshoring Makes Sense for Plastics Manufacturers
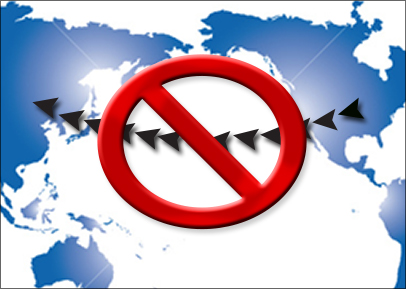
Not long ago offshoring was a standard business practice for a plastic manufacturer (a group that uses plastics in its final products) looking to increase profit margins– but the times have changed. The advantages of outsourcing are disappearing with business analysts exposing the hidden costs of outsourcing goods and services, and many companies are taking notice and exploring the benefits of reshoring. Reshoring or “backshoring” refers to a company’s manufacturing movement from an offshore location back to their home country. Reshoring is primarily an American movement since U.S. plastic manufacturers have been much more aggressive with offshoring practices than Asian or European countries. Global economic changes affecting the financial cost of offshoring, along with other marketability and efficiency considerations mean that reshoring now makes business sense for many companies.
The Problem with Plastics Manufacturers Going Offshore
Offshore production can increase risks for plastics manufacturers associated with shipping, quality control, management and customer loyalty among others. Some firms set minimum cost savings (usually around 15%) before moving production offshore, but today’s manufacturing environment makes this figure difficult to obtain, leaving companies to guess their cost or discover those figures the hard way. Companies looking to move their production lines offshore should consider the following issues:
Shipping Issues/Costs
Overseas shipping is expensive due to climbing transportation costs (associated with a spike in oil prices). Offshore shipping also carries with it the added risk of product damage because of longer transit times. Furthermore, foreign shipments also run into the customs barrier, which creates longer lead-times. Emergency air freight can also carry a hefty price tag. Speedy shipping is important to many clients and some plastics manufacturers may not want the added cost of overstocking their U.S. warehouses in order to compromise on this issue.
Plastics Manufacturer Quality Problems
Manufactured products from various other countries have been reported as having a higher defect per million number than the United States. A Six Sigma process improvement methodology allows a 3.4 defects per million rate (or 0.0000034 percent) as being within acceptable limits. The New York Times recently reported that a solar panel manufactured in China had defect rates ranging from 5-22%. In the United States, quality and compliance standards for plastics manufacturers and other producers of goods and services are among the highest in the world and more easily monitored.
Increase in Overseas Wages
The cheap minimum wage requirements overseas used to be enough for many plastics manufacturers to consider offshore production. But according to Boston Consulting Group, Chinese pay and benefits are up nearly 20% from 2001, during the height of the outsourcing movement. Most of Asia has seen similar wage rate increases. Effective in-country labor strikes have benefited the overseas workers, while cutting into the bottom line of American companies using off shore outsourcing strategies. According to a study from the consulting group Hay Firm, the salary for senior management in emerging markets such as China, Turkey and Brazil now either matches or exceeds America and Europe.
Overall Efficiency
Managing operations in locations far away from where the demand lies hinders planning, forecasting and overall flexibility, all of which drive up costs. Many plastics manufacturers choosing to reshore cite inventory carrying costs and supply disruptions. Companies that reshore routinely see an average of 50% reduction in their inventories which increases inventory “turns” greatly. These reductions can occur because of shorter lead times and more certainty with delivery dates and quality. Faster shipments and order fulfillment also helps improve customer satisfaction and client retention – and to satisfy spikes in production requirements.
Problems with Customer Loyalty
Companies know that it is cheaper to retain a current customer than to obtain a new one; therefore, customer loyalty incentives are an important part of any business strategy. But cultural proximity tends to increase customer loyalty, leaving offshore manufacturing at a disadvantage in this area. Some companies try to hide their outsourced call centers by training their employees to claim they are working from false locations. Heavy accents can be difficult to understand over the phone, and some customers may resent being lied to about where a call center is located. This example is the beginning of the breakdown of the relationship between the customer and the company. The same principle can be applied to “made in America” content labeling, which informs end buyers of where the end products and/or the components were made. If there is price parity, or even a slight difference, a study cited by Inc magazine shows that Americans will actually buy American-made products.

Investments in information technology, the adoption of total quality management practices, and the use of robotic systems have helped the U.S. dramatically increase its overall manufacturing value. Even though China and the U.S. are fairly close in manufacturing output dollars, the U.S. produces this at 10% of the workforce used in China. A plastics manufacturer can now consider bringing production back home with the potential for more competitive efficiency.
Advancements in Automated Manufacturing
The United States has increasingly adopted advanced manufacturing techniques to improve efficiency and keep costs low enough for companies to consider reshoring. Once automation is in place, the cost of adding full time (24/7) manufacturing capacity (as a percent of overhead) drops dramatically. Robots can also now work with incredible dexterity at low costs to manufacturers. (For around $22,000, companies can purchase an easy-to-operate robot that can work right next to human assemblers, expanding their productivity). Creation of more efficient work cells are also contributing to less material movement, less worker errors and more productivity. Nascent techniques like 3-D printing, which can replace some manual assembly, are being implemented. These sorts of automated manufacturing systems are mainly used now for prototyping and complex parts, but in the future they may produce final products for plastics manufacturers on a larger scale.
Calculating a Plastic Manufacturer’s Reshoring Costs
Companies considering either outsourcing or reshoring, should consider several important business costs for both Asia (or other outsourced country) and the United States:
Supplier search time Supplier search site visits Supplier personnel Account management team personnel Software compatibility Any upfront equipment costs Production start-up Raw material inventory | Minimum production runs Cycle times Transit time Transportation containers Other packaging/shipping costs Quality resolution communication Finished goods inventory storage Production demand fluctuations |
(B and B Molded Products has a “total cost” worksheet that can be used to examine true offshoring total costs, as well as a direct comparison sheet and a process that helps analyze the cost benefits of reshoring. ) Companies are beginning to realize that managing production at a distance has weakened their quality control capabilities and isn’t as inexpensive today as their initial cost assessments may have portrayed. Offshore manufacturing has damaged many plastics manufacturers’ ability to meet customer expectations in a variety of areas. Conversely, bringing manufacturing closer to home improves a company’s flexibility and allows them to meet diverse customer demands with high-quality products and quick turn-around times. Reshoring is not only good for individual companies, but it also helps bolster the U.S. economy by creating jobs, reducing the severity of recessions, and helping to balance the trade deficit. Improved U.S. manufacturing efficiency makes reshoring at least a competitive consideration.
Business Benefits for a Plastics Manufacturer Deciding to Reshore
So in summary, a plastics manufacturer deciding to reshore production will have:
Faster delivery times. Lower transportation costs. Fewer product defects. Economic stability. Established worker safety compliance standards. | Established materials safety compliance standards. The benefit of a “Made in the U.S.A.” label. The satisfaction of knowing they are supporting the US economy by employing American workers. More world-class manufacturers to choose from. Improved customer service. |
Many plastics manufacturers or other large firms deciding to reshore are only beginning with small production lines and keeping a larger amount of their work overseas; however, the movement to reshore is catching more companies’ attention, with those making the switch enjoying the benefits of positive media coverage. Reshoring may not be the cheapest business strategy for all companies, but perhaps it is the right one.