Optimized Manufacturing For the Custom Plastic Injection Molding Environment
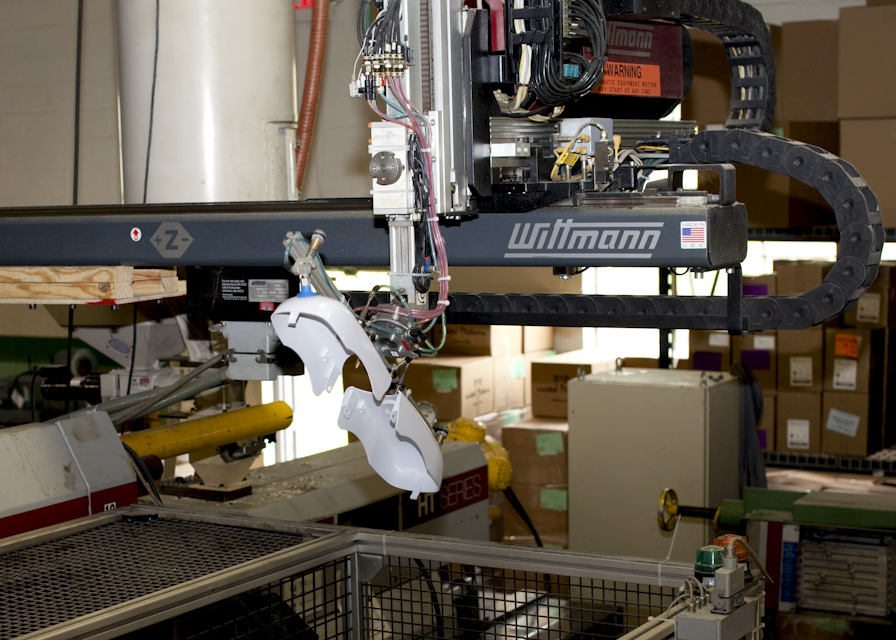
Our custom plastic injection molding operation is geared toward the continuous improvement methodologies needed to lower costs, increase quality and exceed our delivery commitments. This is accomplished by an emphasis on making our manufacturing processes as efficient as possible. This includes input and evaluation from our manufacturing staff in virtually every phase of the process from initial review and project estimates (unit cost, tooling, life cycle maintenance, etc.) through end customer satisfaction. We are constantly searching for realistic and high value process improvements that can be executed on behalf of our customers. To attain this we regularly:
- Test, document and review our manufacturing processes and approaches
- Research new methods, materials, equipment, training approaches and skills
- Find and compare (benchmark) our processes against similar manufacturers in areas of cost reduction, quality improvement and efficiency
- Quickly resolve any internal issues that may impact cost or quality either on a short or long term basis
Key Areas For Manufacturing Support
Our manufacturing resources are charged with both internal and external support, with a goal of anticipating and solving potential problems before they could impede our manufacturing output. Areas we address during this process include:
- Mold manufacturing methods
- Material characteristics, cost, supplier profile and performance
- Tooling and mold preparation, performance and longevity
- Specific mold elements such as runners, gating, nozzles, cooling, clamping pressures, clearances, cavitation, parting lines, maintenance aids and support
- Material/product handling and transfers in and between work cells (part staging, ejection, queuing)
- Assembly methods and manufacturing efficiency for final assembly