Evaluating the Impact of Part Design on Injection Molding Processes
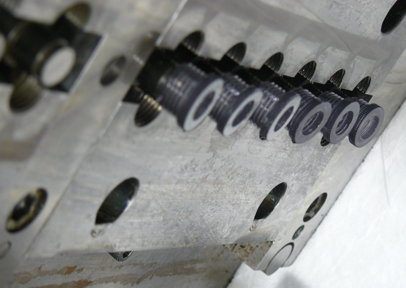
Something that many manufacturers overlook, while asking their injection molding supplier to control finished part costs, is the supplier’s ability to help evaluate the impact of part design. While molders may not be considered product engineering experts, the intimate relationship between product design and production cost is something they must become adept at mastering in order to survive. Taking advantage of this very practical knowledge base can result in hefty cost savings – even if product design/ tooling production has already taken place.
Product Design Cost Reduction Factors
There are many factors in driving finished injection molded part cost, but one of the most important is the basic product design. This includes a variety of factors, including:
Material selection including stress/strain limits, impact resistance, fatigue over time and pressure, thermal characteristics, flammability, flow properties, environmental considerations (recycling/disposal, degradation), flexibility (for example, ability to use additives to change stiffness, color, UV resistance, reinforcement, flame retardants) among others
Part characteristics and execution difficulties including geometries, stress points, support level and type, need for user safety, performance characteristics
Design for automation and manufacturing ease, both general characteristics and those that might relate to a specific manufacturing situation including press capability, material handling, mold design, cycle times, run-length and maintenance (approaches and intervals)
Material Selection
While there are countless polymers available for the part designer, in a practical sense, most designs will dictate an immediate sub-selection based upon the application and performance of the product, manufacturing constraints, experience, regulations/certifications/agency approvals and of course cost.
Since plastics are typically compounded from simpler elements or structures such as monomers or co-monomers, there are many ways to alter the performance of these polymers by adding different base elements, use of additives that can change chemical behaviors, by changing base element proportions or other characteristics of similarly structured materials, the processing and end use characteristics can vary greatly. Carrying the previous example much further, there are categories of “ultra high” molecular weight polyethylene that can resist surface damage, chemical decomposition, etc., but are hard to injection mold because their higher weight building blocks impede flow at normal injection molding temperatures and pressures. As just one example of the different trade-offs that should occur, the following chart contrasts basic mechanical properties of two broad classes of polymers.
Material Characteristic | Crystalline Polymer 1 | Amorphous Polymer 2 |
Chemical Resistance | Higher | Lower |
Shrinkage | Higher | Lower |
Warpage | Higher | Lower |
Tensile Strength | Higher | Lower |
Tensile Modulus | Higher | Lower |
Elongation | Lower | Higher |
Creep Resistance | Higher | Lower |
Flow | Higher | Lower |
Maximum Exposure Temperature | Higher | Lower |
Density | Higher | Lower |
1 Like polypropylene, polyethylene, nylon, Polybutylene terephthalate (PBT), Polyethylene terephthalate (PET) | ||
2 Like Polycarbonate, Acrylonitrile butadiene styrene (ABS), Polystyrene, Thermoplastic polyurethane (TPU), Styrene-acrylonitrile (SAN), polyphenylene oxide (PPO) | ||
Source: Rosato, Donald V. and Dominick V, Injection Molding Handbook, 1995 |
Part Characteristics
As part design increases in complexity, so typically do production costs. “Part characteristics” can mean a variety of factors including:
- Hard-to-achieve base characteristics that challenge material or process limitations
- Factors which slow manufacturing cycle times, increase base material usage, or have other cost impacts
- Choices which add to long-term/overall costs including quality costs, shipping/packaging, brand reputation/repeat purchases, etc.
Some of the more common design considerations often stem from this basic product structuring. These may include:
Wall Thickness, which depending upon the total unit production size, is a balance between product cost, product performance, and shipping/transportation cost (both raw material and finished goods). It can also affect user value perception (if the product ends up being perceived as poorly made). If incorrectly specified, it is also one of the key drivers in production problems ranging from mold redesign to slower production line rates. The designer has many options that can positively influence these factors such as using ribs, curves, corrugations and posts to stiffen the part without increasing actual wall thickness.
Unintended Flow Narrowing, which can occur when designs cut off or narrow the flow paths or channels for the thermoplastic material. This is often a hidden issue until the final prototype stage as even seemingly benign design choices such as a tighter/thinner corner radius can impede material flow. The potential for creating voids or under tolerance parts are not limited to corners and can include many design techniques such as:
- Providing angled transitions or tapers that help conduct the flow of the material from the mold runner
- Using the proper radius to thickness ratio for corners and other areas where multiple planes or features meet (as noted above), and avoiding sharp corners when possible favoring gentle radii (rounding)
- Not reducing thickness more than is viable for the shrinkage property of the material used
- Using the proper computer-assisted flow simulation algorithms which can take a lot of the guess work out of removing flow restrictions in a given design.
Tolerances, the maintenance of which often start with mating the right base material to the allowable dimensional variation between finished parts or sub assemblies. In general, the less deviation that can be tolerated, the lower the shrinkage of the material to be used. Also the designs feature can affect dimensional outcomes. For example, it may also be wise to “decrease” tolerances where alignment of multiple parts may be critical (for instance hinges, sliding components, snap together areas, undercuts, etc.).
Design for Automation
Design for manufacturing/assembly (DFA or DFM) has been around in various forms since the dawn of the assembly line. However, few parts are totally optimized for automation because of the trade-off between automation cost, units produced, part life and cost and availability of labor. Still a critical design review by the injection molder can be used to test the value of applying as many of the DFA/DFM techniques that are cost effective and feasible. Here are a few common approaches:
- Parts reduction via consolidation, which can apply if molding capabilities allow. This can include evaluating how much movement the components may have, if there are multiple material types (such as inserts), the number of variations or customizations or if the components may need disassembly for servicing or replacement in the future.
- Assembly order, which is done to support automation which costs more if parts must constantly change in orientation, or if they follow an assembly order that is not an easy-to-execute sequence (i.e. parts are added more randomly rather than in a specified order such as on top of a fixed orientation part base.)
- Reuse of the same common parts such as fasteners, mounting plates, inserts, etc. rather than specifying new or different parts that have similar functions.
- Use of lowest labor content means of fastening such as welding, adhesives, mechanical fasteners, snap fitting, etc. If mechanical fasteners must be used, they should be self-threading rather than a “bolt and nut” configuration to lower parts count and assembly steps. Similarly “retention” approaches can be used (in addition to snap fit) that allow parts to “hold themselves” together and eliminate the need for joining methods of any kind.
- Use of alignment and part orientation features to help guide the parts together during the assembly process can support both manual and automated assembly procedures. Also, making sure parts have smoother designs that eliminate the chance for catching or other restrictions can aid assembly.
- Trying to avoid secondary operations such as machining, finishing, painting, really decorating of any type also is a reasonable DFM strategy
In the end, using the practical knowledge of your injection molder to help optimize product (and mold) design can be tremendously valuable. It can also provide a continuous feedback to help with future product design iterations. Of course, information sharing with your molder helps improve this process such as field performance, warranty/repair profiles, shipping timelines, agency requirement updates, etc.